Opinion piece
Making Material Changes in Buildings
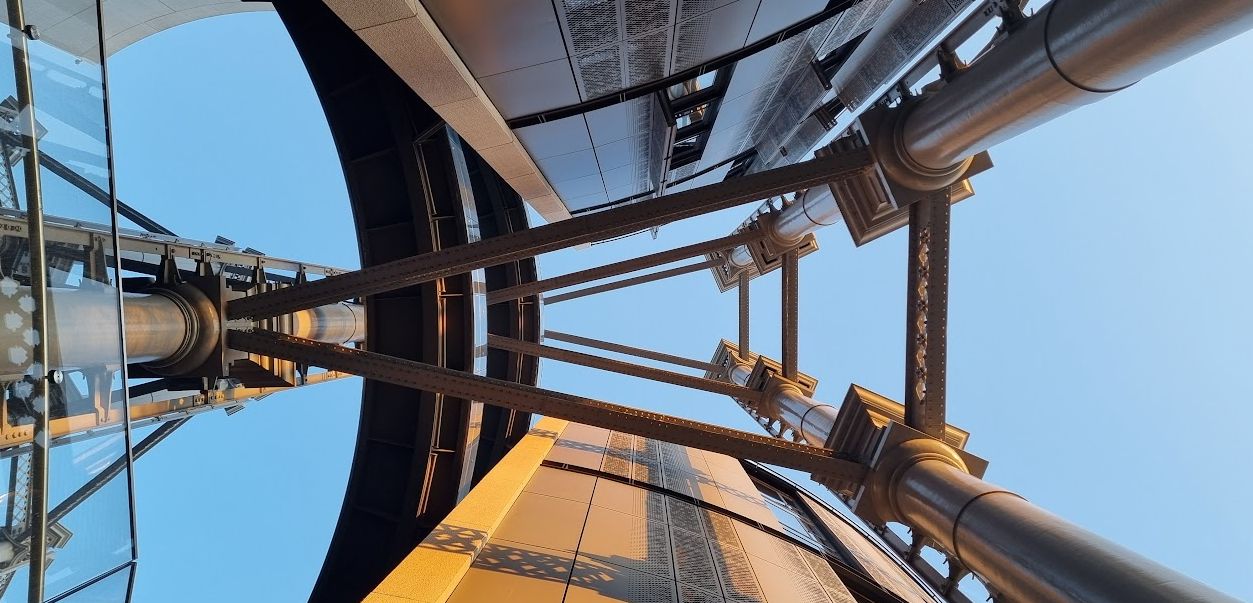
An opinion piece article by Will Arnold, Head of Climate Action, The Institution of Structural Engineers (IStructE)
Carbon in buildings
Buildings are a good thing. They bring people together, keep them warm, and give them places to be useful. But as we are all painfully aware, the construction, operation and destruction of these buildings has been pushing us beyond our planetary boundaries for quite some time now.
But we can’t just stop construction altogether – as buildings are a good thing. So instead, we must learn how to construct them whilst minimising our damage the environment. (in fact, eventually we must even learn to construct buildings that heal the environment, but one thing at a time.)
Historically, most of the carbon emissions from buildings have been due to their operation (heating, lighting, cooling etc). However this is changing. There are plans for reducing this embodied carbon – electrify, insulate, and generate on-site – and as such, the largest contributor to a modern building’s emissions is the materials used in its creation – the embodied carbon.
Most of the embodied carbon emissions are due to the construction of the building structure. In fact, the concrete and steel industries combined make up over 15% of all global emissions[1]. And as the structure of a building typically comprises of just two or three materials; if you can focus on decarbonising these few pieces of the puzzle, then you can make very large carbon savings very quickly.
As such, I believe that the decarbonisation of building structures is one of the most important challenges facing our industry today.
Decarbonising building structures
My mantra for low carbon design is simple: “Use less stuff”.
The quickest way to reduce the carbon emissions of these building structures is simply to use less stuff – use less material, do less construction. This results in a tangible drop in emissions today, not at some point in the future. And it’s today that we have a climate crisis on our hands.
The quickest way to realise such carbon savings is through reuse (as you don’t need to build anything new), but even for a new project there are usually plenty of opportunities to use less material.
Putting columns closer together, building to sensible scales, and giving the engineer sufficient space for nice efficient beams will all go huge ways towards reducing the amount of material used on a project. The exemplars we see show that you could halve your material use through such ingenuity and creativity.
The role of material decarbonisation
However, material efficiency can only get us so far. And so at the same time as using less stuff, we must also decarbonise the materials that we use to build with. Maybe we can halve our emissions through using less stuff, but the IPCC says that we must halve emissions by 2030. What will we do after that?
So whilst the job of today’s building creators is use less stuff; the task of material scientists, process engineers and manufacturing behemoths is to create materials that will enable us to go below half. If we want lower carbon materials ready to use on all of our projects by 2030 (not only the trailblazers), then these materials need to be in R&D stage today. Industry needs to be investing in this decarbonisation at war-time (or pandemic-time) levels – getting things out of the lab today, scaling up for use on exemplar projects in the next few years, and being available to the mass market by the end of this decade.
Realistic speed of progress
We should be careful to recognise that materials will not decarbonise overnight – hence the need to continue to use less stuff today. Over the last century, humans have been rapidly fine-tuning our industrial processes that create the materials that we use. But this fine-tuning has been based on minimising cost, and so a paradigm shift towards also minimising planetary impact is like trying to change course in the world’s largest ship – it needs a gargantuan effort, and change happens slowly.
When you then consider the pace of change required by the IPCC’s 1.5°C pathway (halving emissions by 2030 and getting to zero by 2050, equivalent to reducing by 10%/year), you see that this decarbonisation is simply not happening fast enough.
I don’t know of a single manufacturer that’s claiming that their production emissions will be 10% lower this year than they were last year. It simply takes too long to build the facilities to trial and scale the low-carbon technologies we need to see happen.
Material distractions
Worse than this, there are unfortunately a lot of products being marketed as ‘low carbon’ whilst being anything but that. Looking at the ‘low-carbon’ concretes and steels on the market today, you see that the majority of these technologies rely on substituting virgin steel and virgin cement, with scrap steel and ‘cement replacements’ (typically waste by-products from coal-powered industries). This is great in theory, except that globally we consume three times as much steel as exists in scrap form, and eight times as much cement as exists replacements.
So if you buy materials that have a higher-than-average amount of cement replacement or scrap steel in it, then your project’s emissions will be lower-than-average, but you’re not reducing global emissions. You’re simply moving these limited resources from somewhere else in the world (where they probably would have been used anyway) to your own project location. In fact, if you use any fossil fuels to transport those materials then instead you’ve probably increased global emissions.
So we have to learn to distinguish truly low-carbon innovations from those that simply have good marketing campaigns. We have to help the materials industries to decarbonise, but we also must demand that this happens quickly, and transparently.
Dual challenges
In summary, is clear to me that there are two parallel challenges for the construction industry:
- We must decarbonise our materials, as we cannot get to net zero with the current ones.
- We must reduce the amount of material that we use, as the industries cannot decarbonise fast enough.
Those working to finance, commission, design, construct or maintain buildings today must concentrate on Challenge Number 2, and work to use less stuff. We must also be cautious when being offered ‘low-carbon’ versions of materials today, as these aren’t always what they seem.
At the same time, those working for producers, manufacturers and materials research labs must now drive a rapid response to Challenge Number 1. We cannot get to net zero with today’s materials, and we cannot simply stop building things all together.
The construction industry is relying on these developments to happen today, in order to enable us to keep decarbonising past 2030.
[1] Cement is 7% of global CO2 emissions: https://gccassociation.org/news/global-cement-and-concrete-industry-announces-roadmap-to-achieve-groundbreaking-net-zero-co2-emissions-by-2050 and steel is 9%: https://accelerator.chathamhouse.org/article/achieving-net-zero-steel
I’d also invite you to join us for a discussion on this topic at the first Futurebuild Big Issue webinar session “Materials must change” on Wednesday 27 April 12 pm (GMT).
Share this article:
Read more:
IF WE HAVE THE ABILITY, WE HAVE A RESPONSIBILITY
Opinion Piece IF WE HAVE THE ABILITY, WE HAVE A RESPONSIBILITY Opinion piece by David Ing, Managing Director, Fabrick It feels like the industry is
The next government must get behind the circular economy
Opinion Piece The next government must get behind the circular economy Opinion piece by Ben Goodwin, Director of Policy and Public Affairs, IEMA There are
Shaping The Future Of Sustainable Construction With Unprecedented Impact
Press release FUTUREBUILD 2024: SHAPING THE FUTURE OF SUSTAINABLE CONSTRUCTION WITH UNPRECEDENTED IMPACT Despite the challenges currently faced by the industry, Futurebuild continues to push